The Main Cylinder
"Here you go 007, a little something I put together for your latest mission against G.N.O.M.E. Hopefully you won't break this one, as it cost rather a lot and you know how our budget was cut recently... Anyway, it looks similar to your standard, ordinary Dremel but I've made some extra special modifications! I've increased the size and power dramatically, added a much, much larger cutting disk, which now operates flat rather than perpendicular to the body of the tool, oh, and I added a guard behind the blade. Uh uh! Don't touch that button, 007!"
"Why, what does it do, Q?"
"It turns it on, 007!"
"You know, Q, this looks an awful lot like an Angle Grinder...?"
"Oh. Hrm. Um...well...just don't break it."
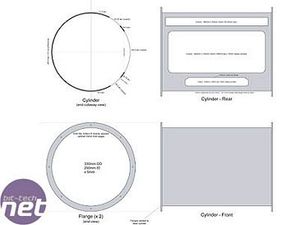
For the rolling and welding of the main parts of the cylinder and end pieces, I was fortunate to have access to a proper engineering workshop with a decent sheet metal roller and welding gear. Unfortunately, I only had a limited amount of time in there, due to the place being fairly busy with commercial contracts that kinda took priority over crazy case modders. This meant I had to work fast to make use of the time and didn't get as many opportunities to shoot as many pictures as I would have liked through having to keep working. Thanks have to go to Markus Serbin, one of the engineers there, who helped me with the welding as I'd not worked with stainless steel before. He's German and reinforces my belief in the quality of German engineering, being more of a craftsman than an engineer.

The body of the cylinder is made from 2mm stainless steel sheet. This was laser-cut, with all the openings being almost completely cut out save for small tabs. The reason for this is that a sheet metal roller
needs material to grip on to in order to roll a curve in it. If the cut-outs had've been completely open when the sheet went through the roller, then the narrow areas on either side of them wouldn't have rolled properly and ended up completely flat. Even doing it this way still resulted in some slight flattening to either side of the reservoir opening (which you'll see later). The tabs were later nicked through with a small angle grinder and the pieces removed.
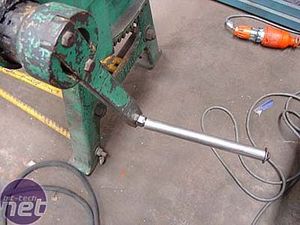
The sheet-metal roller used to curve the cylinder sheet. There is a third roller hiding away behind there and adjustment of it sets the radius of the curve. You just crank the handle and the steel rolls through like the wringer in an old washing machine. Not something you want to get fingers (or other parts of your anatomy) caught in.
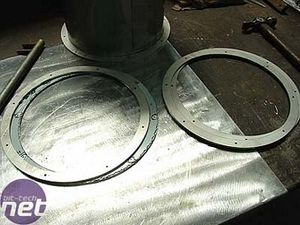
Once the steel was rolled, the laser-cut flanges were fitted on. This required a bit of force and levering, despite the rolling, as the rolled sheet still wanted to spring apart, and had to be forced closed while the flanges went on. The bonus of this, however, was a nice tight fit. In the second pic, you can also see some of the flanges for the end sections of the case.
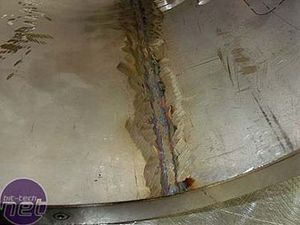
The cylinder was then welded along the join and the weld cleaned up with an angle grinder.
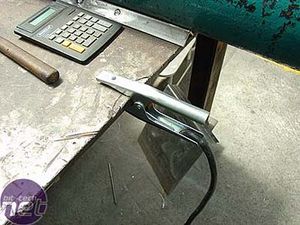
There was some pretty good welding gear at this place. Even the benches were made of steel and earthed, which made the job of welding the cylinder a lot easier.
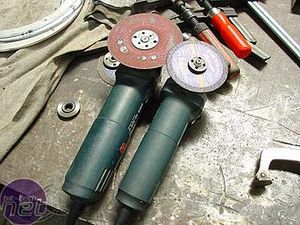
The aforementioned angle grinders. Super-size Dremels!
Want to comment? Please log in.